20.04.20
University of Sunderland producing protective face shields for medics
Frontline health workers in the North East are being provided with protective face shields designed by the University of Sunderland to help protect them during the coronavirus outbreak.
An expert team at the university’s Institute for Automotive and Manufacturing Advanced Practice (AMAP) designed the unique visor, creating the design from scratch with input from regional intensive care unit clinicians.
After the protective face shields underwent evaluation and trialling by medical experts, they were given the green light to produce and supply visors to frontline workers at Newcastle’s Royal Victoria Infirmary (RVI), which has been the main site for coronavirus patients in the North East at present.
More than 200 visors were supplied to staff by the team over the weekend, with more continuing to be 3D printed and assembled, in line with the strict sterilisation procedures necessary for their use in ICU environments.
Alongside their own 3D printing capacities, the team at AMAP have been working with local manufacturing partners, of all sizes, to support and ramp up the production of the protective face shields.
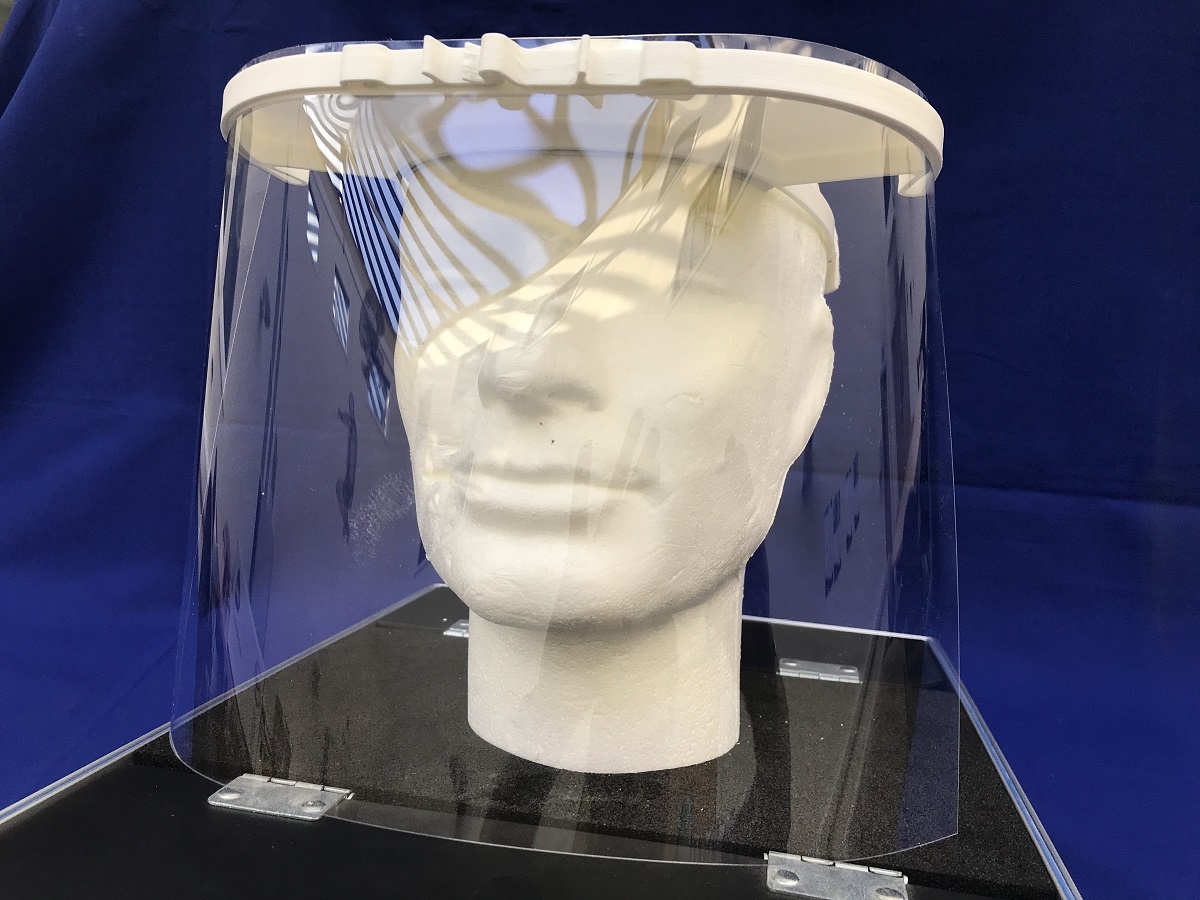
The ICU-suitable protective face shields designed and developed by the University of Sunderland's Institute for Automotive and Manufacturing Advanced Practice (AMAP) team
Roger O’Brien, Director at AMAP, said: “We had a rota of staff working at the University's Industry Centre from 7am until midnight over Easter weekend to produce and assemble the visors to meet the demand.
“In addition to our own efforts, where we have 12 printers running around the clock, there are various manufacturing partners of all sizes of organisation, from small companies to large, who are helping us by 3D printing our frame design, which we then collect from them to process.
“AMAP then quality controls what is produced, sterilises it and then assembles the finished product, adding the visors, forehead protection and retaining straps, all of which have also been sterilised via our processes agreed with the clinicians.
“These are then packed into sterile packaging for delivery, so they can be used immediately upon receipt.”
With demand for protective face shields growing not just in hospitals, but GP surgeries, prisons and care homes around the North East, as well as from the charity Age UK, the team at AMAP have been looking to further bolster production.
The team are currently working with a local manufacturing firm to invest in an injection mould tool which would scale production capabilities up from around 100 face shields a day to many thousands, looking to utilise grant funding from the university’s Sustainable Advanced Manufacturing (SAM) project to support their SME partner with the necessary tooling.
Main Image: Roger O’Brien, Director of the University of Sunderland’s Institute for Automotive and Manufacturing Advanced Practice (AMAP)