03.10.16
The Scan4Safety journey
Source: NHE Sep/Oct 16
Chris Slater, associate director of commercial and procurement at Leeds Teaching Hospitals NHS Trust, talks to NHE’s David Stevenson about the progress being made as part of the Scan4Safety project.
At the beginning of this year, the Department of Health (DH) announced that six NHS acute trusts (see box-out, overleaf) had been selected as demonstrator sites of excellence for the use of GS1 and PEPPOL standards, and collectively received £12m in funding to support the work.
Leeds Teaching Hospital NHS Trust is the biggest hospital group within the Scan4Safety demonstrator sites, and has been on the journey to put stock and inventory management into the heart of the organisation for over a decade.
Back in 2002, the trust became the first hospital in Europe to trade electronically with its major suppliers through the Global Healthcare Exchange (GHX). As a leader on e-enablement for procurement and supplies, Leeds aims to build on its strong foundations as a member of the Scan4Safety group.
Developing consistent data standards
Discussing the early work of the project, associate director of commercial and procurement at Leeds Chris Slater told NHE: “We have about 300+ locations that are all managed by the materials management team, which come under supplies and procurement, and we had about 15 or 18 areas that are now fully inventory managed before Scan4Safety.
“But the issue has always been the inconsistency of the data that you get from suppliers, in the first instance, around product.”
He noted that a good example of this is in orthopaedics where the trust has got the same product, from the same manufacturer, with up to five different barcodes on it depending on the point of manufacture or distribution.
“From an inventory point of view, when you are trying to scan that product out – unless you’ve got every barcode associated in your stock system when you come to issue it – it rejects it,” said Slater. “Then the issue is, of course, that the staff who are using the product or issuing it lose faith in the system.
“Where GS1 and Scan4Safety starts, from my perspective, is getting those consistent data standards into the supply chain. So, for the first time, we are demanding suppliers call the product the same via the GS1 GTIN (Global Trade Item Number) time and time again, so it doesn’t matter whether you are in Derby, Leeds or Plymouth, the GTIN is the GTIN and the system is then capable of holding one GTIN.
“We are looking to push the suppliers towards the end of 2017 to be GS1 and PEPPOL compliant. That is the official request, but I also think we have to be realistic that we will have stock on the shelf – standby items, certainly – that will be of a legacy nature for quite some time.”
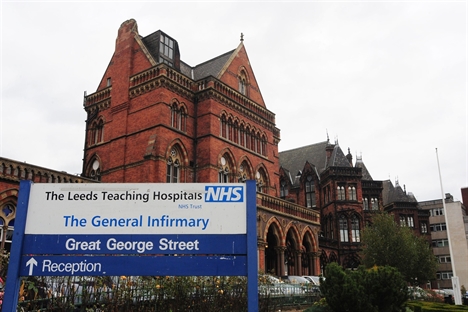
Getting the suppliers compliant
Slater added that the biggest challenge is the GTINs, in terms of getting suppliers GS1-compliant, and recognising that there is a big change that the manufacturers and suppliers need to adopt.
“As a group we are having supplier days, and have a big event coming up in November for both trust chief executives and suppliers,” said Slater. “We are working with the big manufacturers and the big suppliers to, first of all, find out where they are in terms of GS1 compliance, but then are working with them to get the products ready for GS1 and how we get those into our catalogues.
“The GS1 demonstrator project is trying to get a standard established so that we have master information going in at the top level with all the attributes, and then that can get pulled down.”
Inconsistent catalogue management
As well as having a “big piece of work” to get the GTINs in place, the Scan4Safety group is making sure they are capturing the right products and where to increase the number of items on catalogue and on purchase orders (POs).
Slater noted that catalogue management across the NHS is inconsistent and very inefficient, with trusts all having their own systems.
“At trust level there are numbers of people involved with catalogue management when, actually, we just want one set of master data – that is the truth – and then we should be able to pull those down with the attributes,” he said.
“The systems are almost agnostic; it doesn’t matter whether you’ve got PowerGate or Genesis etc. So long as they are capable of handling the data standards, it doesn’t matter which system you actually have. We have got Nexus as our catalogue solution, but there are numerous out there.”
Another aspect that the demonstrator sites are considering is how to capture services at the PO-level, to start doing some deep analysis on the cost of services.
“But that is a little more difficult when you are looking at catalogue management around services,” admitted Slater. “It is one that, collaboratively as a group of six, we are debating as to how far this goes, and what does a service constitute.
“For instance, do we look at temporary staffing as a service? We just have to make sure we don’t put complexity into the process. There are certain areas that you have to agree and can’t capture through a PO process, so you need to have separate controls in place for those. As a group, what we are doing is agreeing on this.
“If we agree when we finally go to roll this out across the wider NHS, what we want to be able to do is have a standard template that the other organisations follow – so we are not reinventing the wheel. As a group of six we are documenting everything we are doing to develop the template.”
Greater collaboration with Carter
The Scan4Safety group meets collectively once a month and is regularly reporting back to the DH on developments.
However, Slater told us that his one disappointment, so far, is that there isn’t quite as strong a link as there should be between the Carter efficiency team and Scan4Safety.
“At the end of the day, the data that we both require is the same,” he said. “I have encouraged NHS Improvement, who are running the Carter programme, to work more collaboratively at the top level with Scan4Safety.
“Leeds is a demonstrator site for Scan4Safety, but it is also one of the 32 trusts in the Carter cohort. So, I’m seeing it from both sides of the coin at the moment.
“Both projects have KPIs and I have encouraged the groups to ensure that the definitions of those KPIs are joint definitions, because you don’t want to be going out to the NHS from the Carter point of view, with one set of KPIs that look to be asking the same question as Scan4Safety but the definition is different. It could get rather confusing.”
Slater said there needs to be a concerted effort to make sure that both projects, which are under the watchful eye of Whitehall and all of the NHS, are encouraged to work together.
Early Leeds progress
After being officially named as a demonstrator site in January, Slater had to start acquiring resource for his team from an almost standing start, which has taken some time to bed in.
During phase 1 of the project, Slater’s team have been establishing the processes within the current organisation and have started to map where it wants to be.
“As part of phase 1 we had to introduce a new patient wristband which was GS1 compliant, and we have got that rolled out across the organisation now,” said Slater. “We are the biggest hospital group within the Scan4Safety consortium. So, everything we do is twice as big in terms of volume, numbers and patients, etc. We have the patient side of things covered and we have mapped our GLNs (Global Location Numbers) thus far, so we have 30,000 GLNs mapped within our internal estates and facilities systems.
“In the next couple of months we are looking at ophthalmology, which would be a greenfield site for inventory management at Leeds, and linking that to not only inventory, but also the instrumentation that we use within that particular area – allowing us to track and trace implement trays through the barcode to clinicians and procedures.
“We have to report in monthly to the DH, and do a benefits tracker. Depending on where you started on that maturity curve depends on when you start to see and realise some of those benefits. I know some trusts have reported early benefits in areas where they hadn’t had any inventory control or stock management where we already had those in place.
“That is one of the reasons I’m going into ophthalmology because it is a greenfield site to us. I want to demonstrate some early results, rather than going back in to areas where we have inventory management, just not at GS1 standards.”
- Derby Teaching Hospitals NHS FT
- Leeds Teaching Hospitals NHS Trust
- North Tees and Hartlepool NHS FT
- Plymouth Hospitals NHS Trust
- Royal Cornwall Hospitals NHS Trust
- Salisbury NSH FT
Tell us what you think – have your say below or email [email protected]